Paddle manufacturing is undergoing a rapid transformation within the ping pong industry, driven by technological advancements and an increasing demand for high-quality equipment. Situated at the heart of innovation, modern ping pong factories provide fascinating insights into the intricacies of paddle production—an essential component contributing to players’ performance.
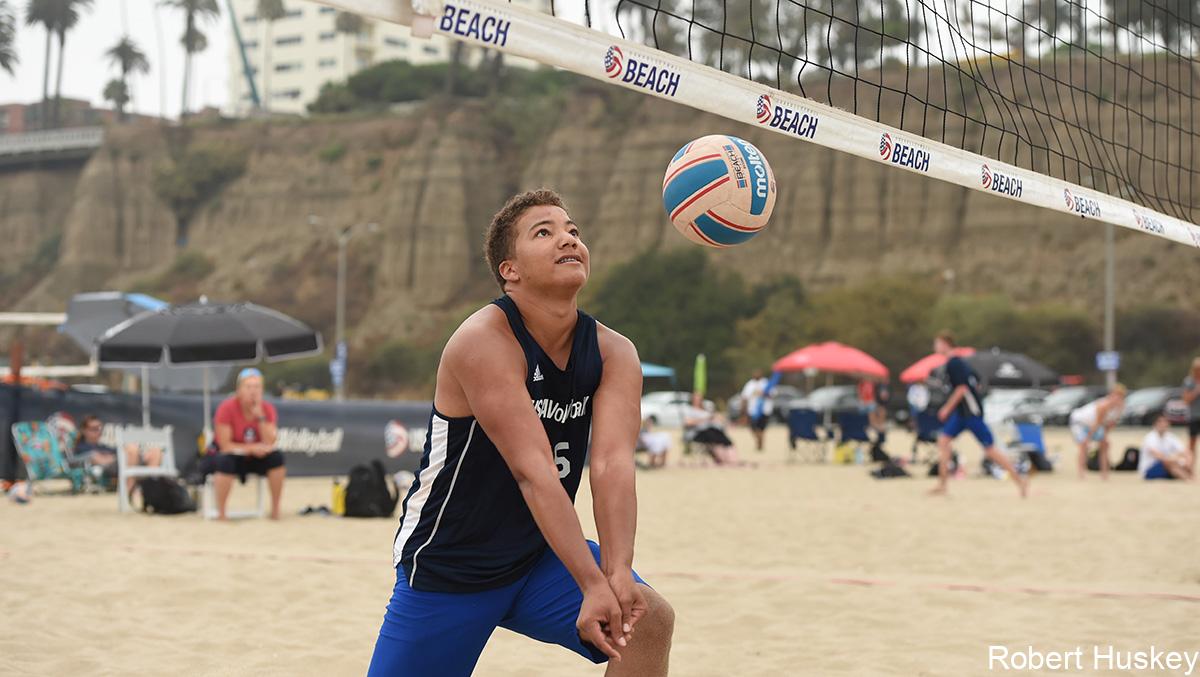
The production journey starts with material selection. Factories prioritize lightweight yet durable woods, such as balsa or ayous, known for providing the perfect balance between speed and spin.
High-end paddles feature carbon or composite layers, enhancing stiffness without compromising weight. Materials ensure that paddles cater to varying play styles, whether for aggressive power shots or delicate spins.
Artisans play a pivotal role, using their expertise to assemble these materials into cohesive units. By carefully layering wooden veneers—sometimes as many as seven—craftsmen optimize the paddle's core. The precision in layering affects performance, as it determines the paddle's responsiveness and control. The core is then meticulously shaped and sanded to achieve the desired thickness and weight, attributes that directly influence the player's feel and control over the game.
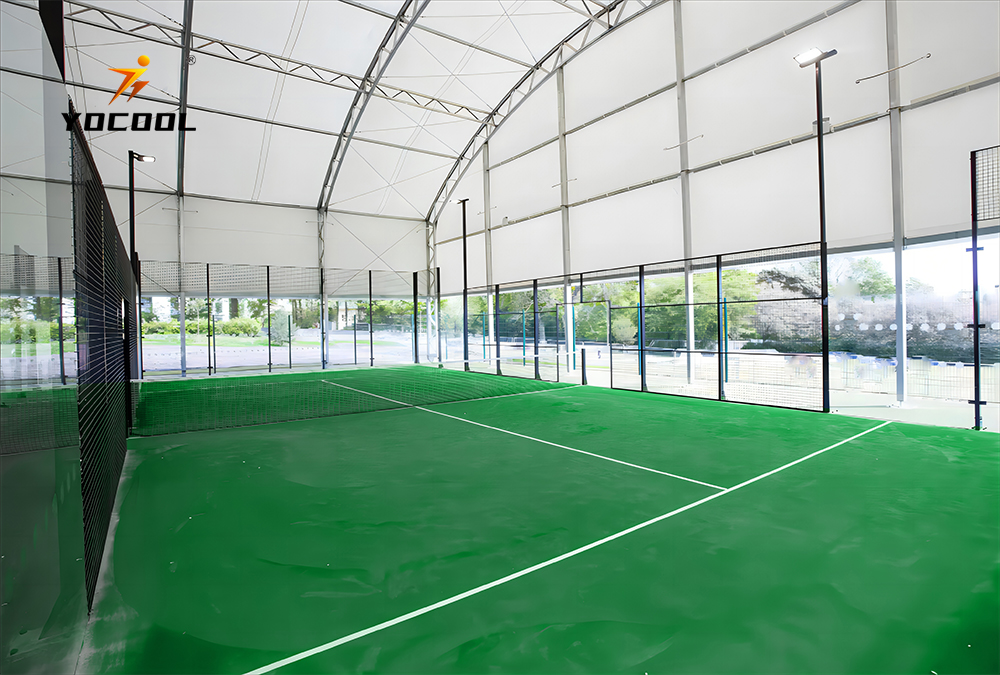
A crucial step lies in the application of the rubber surface, where factories invest significant effort to align with ITTF (International Table Tennis Federation) regulations. This involves cutting-edge adhesives and rollers to ensure an even bond between the rubber and the blade. The selection of rubber, often accompanied by sponge layers, impacts a paddle's grip on the ball, thus affecting spin and speed. Factories test different rubber compositions to enhance grip and deliver a broader range of motion to accommodate various styles of play.
paddle in ping pong factory
Technological integration significantly enhances the production process. Modern factories employ sophisticated CNC machines for precision cutting, which reduces human error and maintains consistency across batches. Automated sanding ensures uniform thickness and smoothness, essential for high-level competition paddles. Some facilities are incorporating AI diagnostics to measure paddle performance characteristics, offering real-time insights into potential design improvements.
Quality control dictates the final product's market readiness. Each paddle undergoes rigorous testing, not only for durability and performance but also for weight and bounce, adhering to strict international standards. Sensors evaluate the angular velocity and impact absorption, ensuring that every paddle meets professional expectations. Factories might also engage athletes for real-world feedback, ensuring the paddles deliver as promised under actual playing conditions.
Importantly, sustainability is taking root within factories, as the industry recognizes its role in environmental stewardship. The adoption of eco-friendly materials and sustainable wood sourcing stands at the forefront of this transformation. Waste reduction programs and recycling initiatives are increasingly common, not only reflecting a commitment to quality but also to global ecological standards.
Ultimately, the production of ping pong paddles within modern factories is a sophisticated dance of tradition and innovation. As the sport evolves, factories continue to meet the needs of players and enthusiasts, ensuring each paddle not only meets competitive standards but also enhances the experience of both professional and amateur players alike. Each step in the process reflects an industry-wide commitment to quality, expertise, and trustworthiness, ensuring players receive the tools necessary to excel at every level of the game.